Bespoke software that improves customer experience and streamlines operations.
We recently worked in partnership with leading specialist in underwater connectivity, CRE Marine, to deliver a technical solution to streamline operations and improve its service to customers.
Working predominantly with connectors, penetrators, junction boxes, termination and cables, the company successfully supports it’s clients’ operations in one of the world’s most demanding environments – the deep ocean.
An essential component of CRE Marine’s operation, is ensuring it is delivering to short delivery schedules without compromising on quality. Reliability and performance are essential to the success of the company, and this is always a key focus for the team.
Working with the Intellicore team was a first choice for CRE Marine's Finance Director, Joe Murdoch:
“I have known Barry for over 10 years and I would not look at any other software developing agency to work with my business – he listens, understands, and provides a huge amount of input that can help the bigger picture, not just thesoftware channel – it was very much a partnership between us and Intellicore.”
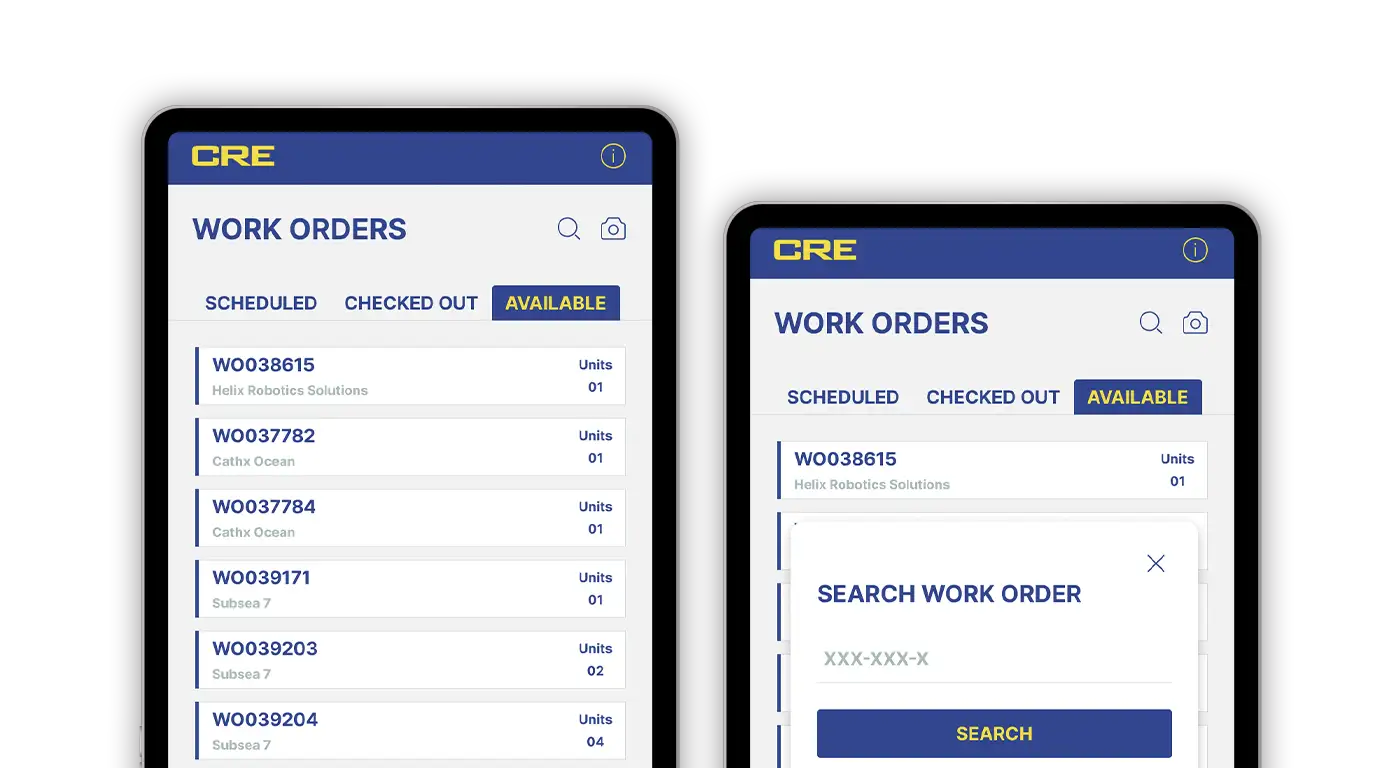
By working closely with CRE Marine, we developed bespoke software that managed the company’s work-in-progress infrastructure that would benefit both the team and the customers.
Despite the recent global upset of COVID-19, the help of the new technology has allowed the company to adapt and work almost seamlessly with the ever-evolving landscape of the industry and the world as a whole.
The new software allows CRE Marine to have greater visibility of work-in-progress, allowing it to provide more up to date information to its customers on deliveries. Essential in today’s busy marine industry.
Joe Murdoch commented on the results of the project:
“With greater visibility of work-in-progress, our customers have commented on the time that has been saved when monitoring deliveries. We also now have a facility to generate internal NCRS (non-confirmed reports) internal and external, which has had huge time-saving benefits for our business.
Intellicore’s ability to create software to our specific CRE requirements and business needs is something that will ensure we have better group communication, tracking and less time spent. Overall, we have already seen the benefits after only a few months of adopting the new software platform.”
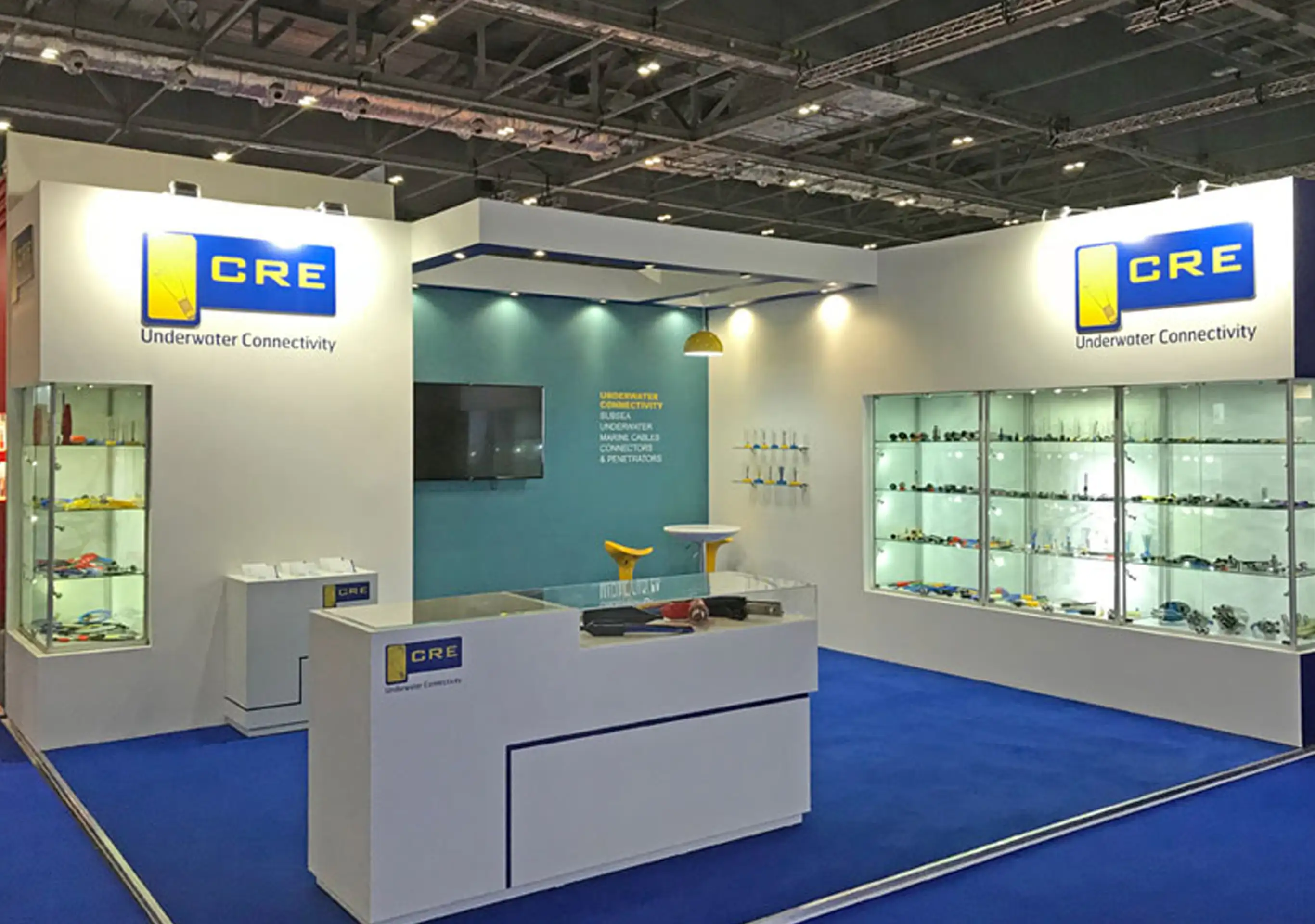
The team at CRE Marine identified that there was a requirement for a bespoke system whereby staff could input changes or modification to operations.
It was essential that the new software had the functionality to:
- Track progress of work orders / work order units
- Pinpoint the location of work orders / work order units
- Improve efficiency through early identification of bottlenecks within the manufacturing process
Intellicore were the first choice of partner for CRE Marine to develop this technology and support in delivering the requirements.
Joe highlighted the importance of finding a solution, and the impact this would have on operations:
“As we have a growing team (60 members of staff at the moment), it was important that we could internally communicate as well as create a process that would allow us to identify and track our products on all levels.”
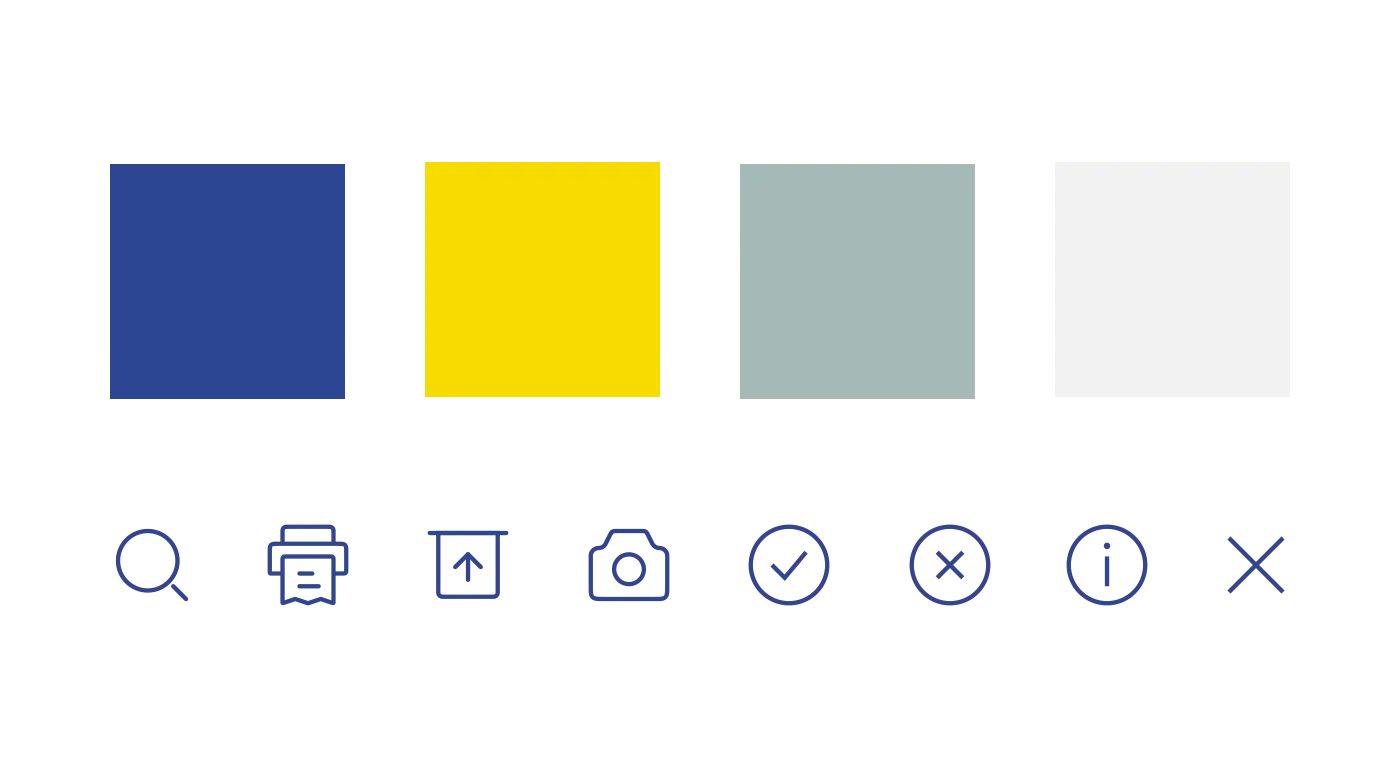
Intellicore built a bespoke solution that synchronises with CRE’s sales orders created within SAGE. These top-level orders are then broken down into Work Orders(specifications) and Work Order Units (unique tracked items), with unique serial numbers and barcodes assigned to each. Work Orders are automatically associated with a set of user-defined Process Steps based on the category of the Work Order. These Process Steps provide a standardised pipeline from the picking of parts, assembly, quality assurance, and through to dispatch; Ensuring that each Work Order Unit is manufactured to the same level and quality.
An accompanying tablet app allows CRE’s technicians to authenticate and log into the solution, providing each user with a personalised list of units for them to complete. This personalisation is based on priority, discipline, as well as being based on any specific scheduling that CRE’s Workshop Manager has put in place from within the portal.
By making use of the tablet’s built-in camera, it provides a technician the ability to scan a units barcode, giving them the confidence that they will be working on the correct Work Order Unit at the correct step in the process.
Taking advantage of the scanning facilities available, the application operates a check-out/check-in system, whereby a Work Order Unit must be checked out by a technician before it can be worked on, moved to the next step in the process, or moved back to a previous step and a Non-Conformance Report (NCR) raised. This provides an in-depth timeline of events, who did them and when; Allowing for management to obtain an accurate progression update as well as a physic allocation of a Work Order Unit in just a few clicks when required.
As the system has matured and become critical to CRE’s operations, they have recognised the desire to continue to invest in the platform. With further additions being implemented including;
- A dedicated portal for managing CRE’s QHSE processes.
- The introduction of Production Cells that helped facilitate the need for their technicians to work in isolated bubbles during the Covid-19pandemic, allowing for CRE to remain operational whilst also minimising the risk to their staff’s safety.
- A portal for their customers to view their orders, the current progression of any active orders, and the ability to raise their own NCRs should they be required.
- An upcoming Supplier portal, that will allow their suppliers to access and action an NCR raised in relation to them. Allowing for the supplier to reconcile and resolve the NCR to CRE’s satisfaction.
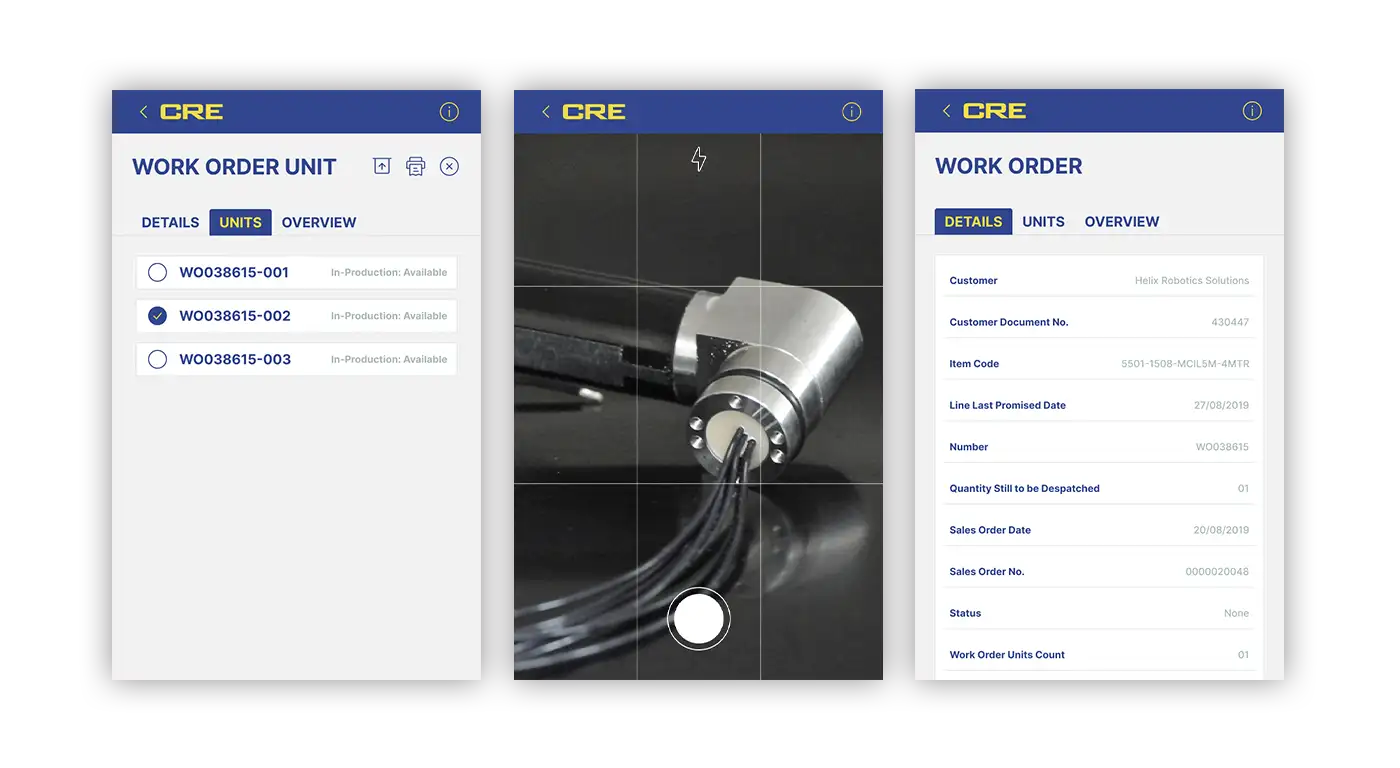
Subscribe to the Intellicore Newsletter
Sign-up and get frequent technology insights on topics including intellectual property and software development, security tools and integrating with API, delivered to your inbox.